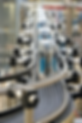
UNILEVER
Autarky Automation and Schuco help
Unilever boost productivity and cut maintenance costs.
A specially developed puck reject, return and store system, designed and manufactured by Autarky Automation and based on Schuco modular conveyor components, is playing an important role in helping Unilever increase productivity and reduce maintenance costs.
Installed at Unilever’s Home and Personal Care factory in Leeds, the puck reject, return and store system forms part of an integrated high speed filling, capping and labelling line used for a wide range of leading brand roll-on deodorants, which are sold throughout Europe.
The roll-on deodorants include brand names such as Dove, Sure, Impulse and Lynx and use Unilever’s unique design of inverted container, where the pack stands upright on the cap. This keeps the liquid deodorant permanently in contact with the roller dispensing ball and ensures that the product is always ready for use.
The production process starts with empty containers being automatically placed in specially designed pucks in which they remain during the filling, capping and labelling operations. At the end of the line, containers are de-pucked and then packed prior to shipping.
At this point they are de-pucked, inverted so that they are standing the right way up and packed into trays of six units in a single pick and place operation, prior to shipping.
Empty pucks from quality control points along the line and from the end of the process are automatically returned to the initial pack orientation unit using the Autarky Automation system. In addition, during product and puck changeovers they are diverted to Autarky Automation’s custom built puck washing, drying and storage facility; this incorporates a stainless steel tank, high pressure cold wash and cold air blower, with storage for up to 900 cleaned pucks.
Chris Fletcher, Project Engineer for Unilever, explains that, “We operate three roll-on lines, of which the first was built specifically for the new design of pack and two were subsequently converted from handling earlier versions of the same products. In each case we have worked closely with design and mechanical engineers from Autarky Automation to develop dedicated systems that meet the unique demands of our particular products and, just as importantly, enable us to minimise our maintenance and operating costs.”
The solution developed by Autarky Automation uses standard conveying and handling modules from the Industrial Automation Division of Schuco Design, including separate lift and alpine units that raise pucks to the washing and storage areas located above each production line. These standard modules are then combined with a range of customised components to create an integrated system with a number of unique features.
Similarly, the problems of trap points that are associated with conventional conveyor to conveyor transfers have been eliminated through the simple expedient of using two Schuco conveyors with a 15 degree offset. This enables pucks to be transferred smoothly, while making the conveyor line safer for operators.
Chris Fletcher believes that the level of service and customer support provided by Autarky Automation has been exemplary. “The experience of Autarky’s engineers has enabled us to develop a cost effective solution that interfaces efficiently with our Profibus and SCADA networks and that reflects our company-wide programme of total preventative maintenance.
Just as importantly, even where we did encounter problems – something that is common with projects of this type and scale – Autarky provided support quickly and ensured that any modifications were implemented without affecting our production output. Overall, they have played a crucial role in helping us build a series of highly advanced and reliable production lines that are capable of sustaining our business in this sector for the foreseeable future.”